下图,介绍了国外、国内除尘技术概况,包括、等,详情如下:
标签归档:环保技术
高炉煤气干式除尘滤袋破损分析与改进措施
摘要:针对高炉煤气实际运行过程中滤袋频繁破损问题,对破损原因进行分析,并提出解决问题的改进措施,有效降底了除尘滤袋运行破损率,延长了除尘滤袋运行周期,取得了良好效果。
1 攀钢现状
攀钢钒公司现有5座高炉,容积分别为1200m33座,1350m31座,2000m31 座,年产生铁约600万t。5座高炉均采用高炉煤气干式布袋除尘技术,布袋除尘效率高达99%以上,除尘后煤气物理显热较高,配合TRT机组可显著提高余热发电量。高炉煤气布袋除尘发电工艺:高炉荒煤气由重力除尘器(DC)进行粗除尘后,通过两组列管式散热器进行降温控制(出口煤气温度小于200 ℃);然后由布袋除尘筒体(BDC)进行进一步精除尘,精除尘后净煤气(含尘量小于3mg/m3)进入TRT透平机发电,或经净煤气减压阀组减压后进入后部高炉煤气主管。
2 滤袋除尘原理
高炉煤气干式除尘的核心是布袋滤料,其除尘原理是通过滤袋纤维截留、惯性碰撞和扩散效应,还有重力自然沉降及静电引力的作用实现除尘。攀钢钒布袋除尘系统采用高强度、耐腐蚀、耐高温复合滤料,在机织滤布表面覆以微孔薄膜制成的覆膜滤布可实现表面过滤。其滤袋表面过滤机理为:基于粉尘层形成有利于过滤的理论,在普通滤料表面覆上一层有微孔的薄膜,薄膜孔径很小,靠微孔筛分作用,能把绝大部分尘粒阻留在膜的表面,完成气固分离的过程,使粉尘只停留于表面且容易脱落,提高滤料的剥离性。
为适应高炉炉顶煤气温度特点,1# 高炉、新3#高炉顶温略偏低,干式除尘系统采用美塔斯覆膜机织布滤袋,持续最高耐热温度200 ℃;2#、3#、4# 高炉顶温偏高且波动较大,干式除尘系统采用耐高温玻纤覆膜机织布滤袋,持续最高耐热温度260 ℃。
3 滤袋运行技术参数
滤袋类型:高温机织布覆膜滤袋;
滤袋规格:BDC-308(m)-12000-250-3-0.4;
使用介质:高炉煤气;
入口荒煤气粉尘含量:8~16g/m3;
出口净煤气含尘量:≤3mg/m3;
滤袋运行差压:≤3kPa;
滤袋过滤风速:0.8~1.0m/min;
过滤效率:0.1um ~0.3um 时过滤效率≥99.99%,≥0.45um时过滤效率≥100%;
滤袋工作压力:0.25MPa;
滤袋工作温度:≤220 ℃〔瞬间(≤30 min)温度≤250 ℃〕。
4 存在的主要问题
4.1 布袋运行磨损穿孔问题
在高炉煤气干式除尘系统运行维护中发现,干式除尘滤袋频繁发生磨损穿孔现象,其滤袋穿孔部位多出现在第一节防瘪环下部位置,布袋破口为T字形或一字形,,破口大小约1~15mm。经分析因高炉冶炼过程中因炉况波动,出现煤气含水量高或煤气温度异常偏低时,极易引起除尘系统滤袋内表面瓦斯灰结垢,形成体积较大的垢块挂在布袋内壁上,引起入口煤气气流方向发生改变,引起布袋局部冲刷磨损;并且,在长时间布袋过滤和加压反吹的过程中,垢块会直接摩擦滤袋,导致滤袋局部强度减弱,滤袋发生穿孔破损现象,导致出口高炉煤气含尘量超标。
4.2 布袋运行出现脱落问题
高炉煤气干式除尘筒体布袋由滤袋、袋帽、压簧、短环链、曲别钩以及卡箍组成,其中从投运后布袋及其配件的检查情况来看,曲别钩的磨损严重,压簧与布袋的垂直中心线在纵向上不一致影响布袋的正常运行。现高炉反吹风清灰模式为关闭过滤阀→打开反吹阀40s→关闭反吹阀延时10s→再次打开反吹阀,合计每个筒体反吹3次,在过滤—反吹过程中,滤袋因升压的高炉煤气气流变化而形成滤袋的胀瘪变化,滤袋的应力变化通过压簧的弹性变化来吸收,经过布袋厂家对滤袋以及配件的检测分析得出反吹压力偏高,反吹时吊挂装置振动较大,压簧与曲别钩进行摩擦造成曲别钩磨损断裂,引起滤袋掉落出现破损。
其次,因炼铁厂高炉顶压调节及顶压信号时有异常出现,运行过程中出现顶压检测值突然大幅下降或检测不到顶压输入信号,TRT 机组静叶顶压跟踪调节失真,易引起干式除尘系统超压保护装置动作,干式除尘滤袋承受较大冲击(滤袋差压≥40kPa),导致滤袋下口松动脱落,滤袋撕裂、曲别勾弯曲磨损、链条断裂等问题,严重影响干式除尘系统安全稳定运行。
5 改进实施
2017年,针对高炉煤气除尘滤袋频繁出现穿孔、脱落破损问题,引起高炉煤气含尘量超标,项目组主要实施了以下改进措施:
5.1 优化除尘滤袋反吹工艺
(1)利用高炉休风机会,对BDC反吹清灰程序进行优化,反吹程序中增设“静置时间”,和“间隔时间”,静置时间范围10~100s;间隔时间范围30~100s,以适当减少筒体自动清灰时间,延长滤袋使用寿命。
(2)反吹清灰是采取风机升压后离线清灰方式,利用阀门进行调节,逐室地产生反向气流,因反向气流和逆压的作用,使滤袋变形收缩、振动而实现清灰。在确保BDC 差压正常情况下,通过在线调整反吹风机入口蝶阀开度,使除尘系统布袋反吹清灰压力由设计值10kPa 逐步降至8kPa,以降低滤袋反吹冲击。
(3)与布袋生产厂家进行沟通,优化布袋易损部位缝制工艺质量,降低布袋反吹破损率。并结合每周2 次BDC 筒体煤气粉尘人工取样检测,有效监控布袋改进后的除尘系统运行质量。
5.2 改进滤袋吊挂装置
(1)在高炉煤气除尘系统布袋吊挂装置的压簧与曲别钩间安装新的防扭转限位卡,强制固定曲别钩,避免发生扭转摩擦。
(2)将布袋吊装链条钩环卡挂在挂钩上,并将挂钩与吊挂支架的角钢焊成一体,避免布袋运行摆动时引起链条钩环磨损断裂。
(3)定期对筒体布袋进行检查预紧,调整布袋压簧拉力至设计值35 kg,防止吊挂装置拉力不够而出现布袋松弛,影响清灰效果。
5.3 优化TRT 静叶调节程序
针对高炉顶压调节异常,除尘系统出现超压放散,引起BDC差压异常偏高问题,项目组对TRT静叶程序进行了优化。
增设透平入口压力和BDC出口总管压力(两点)与TRT 静叶联锁调节程序:当透平入口压力和BDC出口总管压力两点同时高于设定值时,发出声光报警,且静叶调节退出自动模式,转为手动模式,同时静叶开度自动调整到给定值。5台TRT机组具体设定值如表1。
6 实施效果
6.1 煤气除尘系统运行效果
项目实施后,高炉煤气干式除尘系统运行稳定、环保,BDC 平均差压降低了0.9 kPa,滤袋年破损率降低3.62%,高炉煤气含尘量受控,透平机叶片无明显磨损,系统故障率较低。
6.2 经济效益计算
6.2.1 滤袋成本效益
滤袋单价:0.5 万元/ 条滤袋破损更换降低费用=(改进前滤袋破损量-改进后滤袋破损量)×滤袋单价=39万元
6.2.2TRT发电增效
2016吨铁TRT 发电量38.68kW·h/t,2017年1~11月6吨铁TRT发电量39.62kW·h/t。
本项目贡献系数0.3,年铁产量595万t,电价0.342元/kW·h(不含税)计算:
TRT 发电效益:(39.62-38.68)×595 ×0.3 ×0.342=57.4万元
因此,本项目年增加经济效益96.4万元。
7 结语
通过降低高炉干式除尘滤袋破损率率,不仅提升了高炉煤气干式除尘系统运行稳定性和保产能力,降低了系统运行维护劳动强度,并且确保了高炉冶炼顺行,减少了高炉荒煤气放散,为改善生产环境做出了积极贡献。
袋式除尘器的选型依据、常见问题及解决方法
选型依据
的处理风量是指在单位时间内所能净化气体的体积量,根据风量设计或选择袋式除尘器时,一般不能使除尘器在超过规定风量的情况下运行,否则,滤袋容易堵塞,寿命缩短,压力损失大幅度上升,除尘效率也要降低;但也不能将风量选的过大,否则增加设备投资和占地面积,而且浪费资源,不节能。
合理的选择处理风量常常是根据工艺情况和经验来决定的,入口将直接影响下列因素:
1、压力损失和清灰周期
入口浓度增大,同一过滤面积上积灰速度快,压力损失随之增加,结果是不得不增加清灰次数。
2、操作方式
袋式除尘器分为正压和负压两种操作方式,为减少风机磨损,入口浓度大的不宜采用正压操作方式。
3.预收尘有无必要
预收尘就是在除尘器入口处前再增加一级除尘设备,也称前级除尘。
4.滤袋和箱体的磨损
在粉尘具有强磨蚀性的情况下,其磨损量可以认为与含尘浓度成正比。
5.排灰装置的排灰能力
排灰装置的排灰能力应以能排出全部收下的粉尘为准,粉尘量等于入口含尘浓度乘以处理风量。
出口含尘浓度
出口含尘浓度指除尘器的排放浓度,表示方法同入口含尘浓度,出口含尘浓度的大小应以当地环保要求或用户的要求为准,袋式除尘器的排放浓度一般都能达到50mg/Nm3以下。
使用温度
对于袋式除尘器来说,其使用温度取决于两个因素,第一是滤料的最高承受温度,第二是气体温度必须在露点温度以上。
目前,由于玻纤滤料的大量选用,其最高使用温度可达280℃,对高于这一温度的气体必须采取降温措施,对低于露点温度的气体必须采取提温措施。
布袋破损
对布袋取样进行化验,结果显示除破损部位外其他部位的透气量、爆破强度、断裂强度均在使用范围内。同时发现除尘布袋破损部位几乎全在距布袋口20~40cm处,而且是从内部磨损开始破损的。
确定其主要原因应该和反吹系统有关。一是反吹系统的喷嘴不正,造成反吹偏斜;另一方面是反吹压缩空气压力偏大。
解决措施
1、进行喷吹系统改造,改造费用高、周期长,不能在正常的检修期间内完成。经过研究决定在布袋内增加护套,这种办法简单易操作,费用比较低。
2、反吹风压缩空气压力控制在0.25~0.35MPa之间,能够把布袋上的灰清掉即可,如压力过高则影响布袋的使用寿命。可通过观察除尘器进出口压力差变化进行调整,使压力差在控制要求范围内(设计压差
3、调整喷吹程序,把喷吹脉宽从150ms调整为250ms,以减小喷吹的力度,减少布袋的磨损。
压缩空气不足跳停
1.储气罐与提升阀之间的油水分离器因压缩空气脏造成滤芯堵塞;
2.提升阀长时间运行后,密封件磨损,造成压缩空气泄露,致使供气不足。
解决措施
1、增加一套油水分离器,一开一备。当发现滤芯脏时,可以更换另外一套,对脏的这一套进行清洗;
2、除及时更换提升阀密封件之外,还应采取以下措施:提升阀供气压力调节在0.25~0.5MPa之间,保证每个提升阀都能够在规定的时间内动作,压力不宜过高,否则容易使气缸密封件老化,当漏气点增大时,可以适当调高供气压力;保证油水分离器供油,供油速度不能太小,以免失油。另外,在提升气缸的阀杆处加一定量的润滑脂。
3、收尘器能负压或正压操作,其本体结构无任何改变,收尘效率达99.8%以上,净化气体含尘浓度<100mg/m3,除尘器如用于寒冷地区或烟气低于零点时需增设保温加热装置,壳体也要作相应变。
除尘器由链传动装置和切换脉动阀组成,采用高压风机反吹清灰,不受气源条件限制,利用阻力自动控制反吹清灰节约能源延长除尘滤袋使用,严寒地区室内安装其它地区都能在室外安装,可广泛用于机械、铸造、矿山、冶炼、建材、粮食化工等许多部门。
【技术汇】影响石灰石—石膏湿法烟气脱硫系统吸收塔水平衡的运行因素
摘 要:对石灰石-石膏在不同的工作环境和条件下进行了水平衡原因的分析,列出了与生产相关的各种影响因素,为脱硫生产运行管理提供参考。
关键词:吸收塔;低温省煤器的改造;水平衡
0 引言
吸收塔液位在合格范围内是石灰石-石膏湿法运行衡量指标之一,在设计初期,控制逻辑和设备选型可以保证吸收塔的正常液位。江苏南通发电有限公司2015年对所属的2台1050MW燃煤机组进行了低温省煤器改造,通过降低入口温度,提高电除尘的效率。但同时造成吸收塔入口烟气温度大幅下降,吸收塔内浆液蒸发量降低,吸收塔液位处于高液位,水不平衡现象时有发生。
1 吸收塔水不平衡外因
(1)运行人员对测点的选择。目前主控人员对液位测点的选择直接导致液位与实际有偏差(吸收塔上,下各有2个测点,高度差2米,通过压强可以计算出液位),通过液位选点能调出9种吸收塔密度与液位,尤其是吸收塔测点偏差比较大的时候,调点导致液位显示差距非常大,失去了液位参考价值。
(2)受人为因素影响。目前吸收塔启停石膏排浆泵受脱硫公用区调控,脱石膏取决于脱硫现场对石膏品质的判断,从石膏的含水率,滤饼厚度,皮带脱水机的频率,吸收塔密度等综合考虑。由于脱硫人员对石膏含水率无标准,常会发生现场判断石膏含水率不高,而吸收
塔实际密度低于考核值的问题。
(3)受虚假液位影响。在机组启停投油枪或等离子时,易发生燃烧不完全现象,未燃尽的物质进入吸收塔,造成重金属离子或有机物增加,在吸收塔液位表面,发生皂化反应,形成油膜,产生虚假液位。氧化风量设计不合理,多增加的风量以气泡形式流至浆液表面,这会造成液位折算与实际有差异。
(4)受浆液循环泵启停影响。苏通电厂浆液循环泵属于逐级提升泵组,泵组出力各不相同。由于我公司煤场偏小,采购煤种经常变化,入口硫份变化快,浆液循环泵的启停执行次数较多,对吸收塔水位显示产生不小的影响。
2 吸收塔水不平衡的内因
吸收塔塔内是个动态过程,需能保证相对平衡,受外在影响的因素有很多,水平衡被打乱主要原因就是进出水的失衡。
(1)吸收塔的进水。
1)除雾器冲洗是吸收塔主要的进水量,为保证除雾器效果,避免除雾器差压变大结垢,甚至坍塌,我们一般控制8小时冲洗两次,这个属于可控范围。
2)氧化风机出口减温水,氧化风机出口减温水我们是保持开位,运行时不做调整,这部分减温水是可控的。
3)吸收塔供浆。吸收塔的供浆多少受入口硫份,Ca/S比,液气比,PH值,出口硫份等多重因素影响,为保证烟囱出口硫份低于超净排放值,第一要保证浆液与烟气的亲密接触反应,二是要保证浆液的质量。为节省厂用电,往往采用的是尽可能的减少浆液循环泵的台数,而通过加大供浆来维持出口的排放值,导致供浆量偏大,增加了吸收塔的液位。
4)工艺水和冷却水箱每天两次的对吸收塔的事故喷淋,因时间较短,流量可以忽略不计。
5)回收水至吸收塔。石膏排浆泵将吸收塔浆液从吸收塔输送至旋流器,一部分至回收水箱,另一部分至真空皮带脱水机,石膏被排出,有的直接回回收水箱,有的通过真空罐至回收水箱。新增三路水源,第一是工艺水对真空泵的密封水,流量可控。第二是工艺水对滤布冲洗水箱的补水,受浮球阀控制,时刻保证滤布冲洗水箱水位。在脱石膏初期,浆液密度大,浆液中含水相对少,至滤布冲洗水箱的水较后期浆液密度低时少,存在先期工艺水对滤布冲洗水箱补水的过程,增加了部分外来水。第三是工艺水箱溢流或暴雨天气,水会流至预洗涤地坑,会自启预洗涤提升泵,将预洗涤缓冲箱液位抬高,定期开预洗涤外排泵对滤布冲洗,回水至回收水箱。
(2)吸收塔的出水。
1)吸收塔的蒸发量。吸收塔入口的烟气温度对吸收塔内液位有很大的影响,烟温越高,吸收塔浆液的蒸发量也就越大。这个与排烟温度,煤种,低温省煤器的投用有很大的关系。
2)吸收塔脱石膏。吸收塔脱石膏之后产生的回收水再次返回塔内,返回的水量较脱石膏带出去的略低,可控。
3 吸收塔水不平衡的解决方案
(1)巡检现场测量密度的及时性,巡检接班后巡检第一时间至现场测量浆液密度,通过主控对测点的选择,选出与实际最接近的真实液位和密度。同时由于密度有了参考性,对真空皮带脱水机的及时启停提供有力的判据,避免受人为主观看法的不准确的影响。
(2)对重大辅机浆液循环泵和氧化风机再次进行优化,测量每台浆液循环泵的流量,避免单一的光供浆不开泵的现象。对氧化风机的出力重新评估,最好对氧化风机增加变频改造,避免开单台风机出力不足,两台过量的现象。
(3)优化除雾器冲洗的频率,除雾器冲洗在低省未改造之前是对吸收塔补水的一个重要手段。随着低省的投入,烟温的降低,蒸发量大大减少,除雾器冲洗频率也应在保证除雾器差压的基础上适当减少次数。
(4)对吸收塔供浆的优化,INFIT改造前供浆是通过电动阀来控制,PH值下降至某值,开始供浆,PH值上升至某值,停止供浆,某种程度保证供浆能几乎百分百消耗,而INFIT改造后,调阀跟踪PH值,时刻微量供浆。在高硫份时调节很好,但一旦低硫份时,由于持续供浆,造成PH值远超设定值,易发生吸收塔中毒现象。
(5)目前我们优化了在吸收塔高位时脱石膏同时制浆,可以将部分回用水制成浆液,避免回塔内造成水位升高。这种方式只能缓解,维持的前提就是浆液的高消耗。一旦更换煤种,低硫份煤种,供浆消耗一下子降低,浆液无法消耗,两台浆液箱满,回收水还是要打回塔内。同时利用脱石膏的回水再进行制浆,会让浆液的纯度大打折扣,对浆液的需要远超之前,吸收塔液位易超标。
(6)增加对阀门的检查,吸收塔水不平衡最主要的现象就是蒸发量小于补水量,补水量突然增大的原因就是工艺水,除雾器冲洗水对吸收塔系统的内漏,例如浆液循环泵的机封水,除雾器冲洗阀内漏,工艺水对管道冲洗的内漏,甚至工艺水对滤布冲洗水箱补水浮球阀的卡涩,事故冷却水箱浮球卡涩均导致补水量增加.
除尘新技术对燃煤电厂三氧化硫脱除率高达90%
华中科技大学煤燃烧国家重点实验室一项新研究表明,运用我国发明的团聚强化除尘新技术对燃煤电厂进行改造,不但确保烟尘达到超低排放标准,而且可高效协同脱除烟气中三氧化硫,三氧化硫脱除率高达90%。
这是记者26日从华中科技大学获悉的。我国对燃煤电厂有严格的刚性规定,脱硫主要是脱除二氧化硫气体,对三氧化硫排放没有法制性约束。三氧化硫是一个被忽视的危害,是导致能见度降低和加剧雾霾天气的重要原因之一。
张军营教授团队发明的团聚强化除尘技术不同于静电除尘等物理除尘技术,该技术原理是通过特殊的团聚剂,让粉尘细颗粒润湿、絮凝、团聚变成“大胖子”落网,从而有效提高电除尘和对粉尘细颗粒物的捕集效率。由于细颗粒物脱除率的提高,附着在细颗粒物上三氧化硫等脱除率也会得到提高,因此化学团聚技术能协同脱除三氧化硫、重金属等污染物。
张军营说,化学团聚系统改造成本低,适用性广,协同脱除三氧化硫等污染物能力强,能够显著提高协同脱除率,应对不同烟气条件下的三氧化硫脱除。试验证明,团聚强化除尘技术协同脱除三氧化硫效率最高达到90%,且不同负荷下三氧化硫的排放浓度均低于每立方米10毫克。
水泥厂一线二线窑尾收尘器电改袋的应用与改造
随着新型干法水泥技术的飞速发展,尤其是20世纪90年代前期设计的2500t/d以下水泥生产线普遍面临着技术改造,改造后烧成系统的产量会大幅度提高。原配套的窑尾除尘器无论从处理能力还是除尘效率都已不能满足新标准要求,必须进行改造或更换。如何达到新标准的要求,是目前水泥行业亟待解决的问题。
本次改造的特点是施工难度大,技术要求高,由于生产经营的需要,必须缩短工期。为此我们精心策划.大大缩短了施工工期。设备改造后投入运行,取得良好效果。为水泥行业的技术的提升和进步,提供了成功案例。
1.改造技术方案的确定
由于老厂改造必须要考虑现场空间位置的限制,将窑尾改造为的方案一般有:
①拆除原电除尘器,重新上新袋除尘器(“电换袋”),
②保留电除尘器部分壳体和灰斗改为袋除尘器(“电改袋”),
③保留电除尘器部分壳体和灰斗改为电—袋除尘器(电改“电—袋”)。
经过技术分析和论证,某集团的2条2500t/d新型干法生产线窑尾电收尘适用于方案②,即利用原有的电收尘器部分壳体和灰斗改造为长袋脉冲布袋除尘器。
1.1.改造设备设计原理
目前国内的行脉喷式除尘器的主要部件为:清灰系统、净气室、花板、滤袋室、进出风道、灰斗、支架。其壳体由隔板分为若干独立箱室,各个箱体有独立的灰斗,方便实现在线清灰、离线检修。
行脉喷式除尘器的基本设计原理:净化方式为外滤式下进气结构,正常工作时,含尘气体由进风道进入收尘器后,首先碰到进风道中间的斜隔板.气流便转向流入灰斗,同时气流速度变慢,由于惯性作,使气体中粗颗粒粉尘直接落入灰斗,起到预收尘的作用。
进入灰斗的气流随后折而向上通过内部装有金属骨架的滤袋,粉尘粒子被捕集在滤袋外表面,过滤后的净气体在袋内向上运动直到进入净气室。净化气体经过提升阀进入出风道排出。随着粉尘不断的附着滤袋上.滤袋内外压差不断增大达到预先设定值时,脉冲清灰系统工作,向该单元滤袋喷射压缩空气,使滤袋膨胀、震动,达到清灰目的。
以上各项动作均有PLC编程控制完成,行脉冲袋除尘器在使用过程中,由于使用多阀喷吹,滤袋长度可根据场地需要进行调整,节约空间,目前滤袋有效喷吹长度可达8米,大大降低除尘器占地面积。行脉冲袋除尘器喷吹压力小,一般在0.2-0.4Mpa,压缩空气流量大,动能高,清灰效果好。
1.2.其改造方案
把原电收尘器的上箱体顶盖拆除,充分利用原电除尘器壳体,改变除尘设备进出口方式,增设顶部上箱体(含爬梯和顶部喷吹净气室);保留灰斗、箱体部分,新增净气室和喷吹系统及气路。收尘器的净气室设计为16个独立的单元,并设置提升阀实现离线清灰,每个净气室的气体通过提升阀进入出风通道,改造后正常生产运行时出口粉尘浓度≤30mg/m3。
主要技术参数
将原尾排风机Y4-73-11NO25D风机更换为XY4J-DY2100F风机配用的电机功率:YRKK560-6800KW风量为:520000m3/h,全压为:3600Pa
2.方案特点
2.1.采用烟气均流设计技术
由于是收尘器内部布满滤袋,为确保各室气流的均匀,经过计算机模拟通风试验设计的进风均流通道和灰斗导流(二次导流)技术,使各单元室入口流量均匀,各室负荷基本相同,滤袋等寿命使用。
2.2.采用在线运行、可单室离线检修技术
采用在线运行,单室可离线检修,分十六个室,每个室可单独关闭进行换袋等其他检修工作,这样收尘器的随主机运转率高,有一个室的检修对窑系统的影响也不大;
2.3采用低阻、高效技术
①采用合理长径比的滤袋,选择合理的过滤风速,降低滤袋出口流速,使除尘器袋口阻力降至最小;
②合理控制除尘器滤袋底部的气流上升速度,既可降低气流上升时的阻力,同时可以减小含尘气流对滤袋的冲刷,延长滤袋的使用寿命;
③选择高质量的4寸淹没阀,每个阀喷吹22条袋,袋底的喷吹气流压力保证在2500Pa以上,清灰彻底。
④提升阀下的净气排气口风速设计合理,并采用椭圆形排气,减少气流在此处的湍流造成的阻力损失。
2.4.检修及配套技术人性化
①除尘器顶盖检修门装拆方便,同时选用迷宫型密封设计,采用耐高温硅胶密封元件。收尘器顶部设计泛水0.5%,不仅实现机外换袋,而且在顶部不渗漏雨水,确保设备漏风率<2%;
②除尘器顶部设有检修平台,走道本着人性化设计的原则,并满足安全防护规范的要求,以便人员行走及检修工作方便;
3.精心组织施工为确保工程完成提供了保证
该收尘器按照设计需要安装时间为25天,当设备技术改造时正逢业主水泥生产旺季,为了尽可能把业主生产经营损失降低到最低程度,该公司组织安装人员仔细研究图纸,确定安装最佳方案,最后只用18天就完成了改造任务。
为了确保安装质量和工程进度,不打疲劳战,该司在人力.财力等方面都给与很大的支持,现场安装人员分为二班,保证安装人员有充足的休息时间,现场技术人员全过程跟踪,及时解决工程中出现的技术难题:
工程中体现出以人的工作质量保工序质量,保工程质量,为了确保工程工期进度,根据各安装阶段的工作内容.工作程序,持续时间和链接关系编制相应计划,并在实施的过程中经常检查实际进度是否按计划要求进行,根据出现的偏差分析原因,采取补救措施;施工中还要克服天气原因,最终在工程技术人员与施工人员密切配合下,确保18天的进度目标的实现。为生产经营争取了时间。
4.改造效果
设备改造后,经过一年多的投入运行,生料系统和窑系统投料量达到最大值,收尘器工作稳定,收尘器阻力
【技术汇】锅炉脱硫除尘装置改造
摘要:对双碱法原理进行了分析,结合实例探讨了一体化改造的依据、指标以及原则,通过脱硫除尘一体化改造方案的实际应用得出,脱硫除尘一体化改造没有影响到锅炉正常的负荷能力,也未对锅炉的运行效率造成影响,除尘效率超过了99%,脱硫效率达到82%,拥有良好的脱硫除尘效果。
关键词:锅炉,脱硫除尘,改造方案.
1 概述
现阶段,所采用的湿法脱硫工艺多是石灰石/石灰—石膏工艺,此种脱硫技术是利用钙基脱硫剂吸收烟气中含有的SO2物质,并且产生CaSO4以及CaSO3物质,由于这两种物质拥有相对小的溶解度,经常导致脱硫塔和相应的输送管道发生结垢问题,使得装置出现堵塞。
堵塞现象的出现会对系统运行带来极大影响,甚至会使得整个锅炉系统的运行受到影响。而要想防止上述问题的发生,采用钙法脱硫技术时一般均要求加设上强制氧化装置,即曝气装置,这样会导致系统的初装投资极大增加,而且系统运行过程中所需成本也显著增加。若是采用性能较为优良的钠基脱硫剂吸收烟气中的SO2物质,所需原料成本较高,产生的产物也较难进一步处理。通过采用双碱法烟气脱硫技术,则能够有效的解决上述问题。
此种工艺技术是利用钠基脱硫剂完成脱硫作业,因为该种脱硫剂拥有相对强的碱性,在吸收SO2以后得到的产物拥有较大溶解度,可以有效的避免结垢以及堵塞问题出现。并且,所得的产物会排至再生池之中,再利用Ca(OH)2对脱硫产物进一步还原处理,得到再生的钠基脱硫剂,确保脱硫剂可以循环利用。采用双碱法脱硫技术能够有效的减少初期投资费用,同时还能降低系统运行成本,非常适宜应用在一些中小型的锅炉脱硫改造之中。
2 双碱法脱硫工艺原理
其是将NaOH溶液当成是启动脱硫剂,把事先配置好的NaOH溶液直接的打入脱硫塔之中,通过洗涤方式有效脱除烟气之中含有的SO2物质,所形成的产物被输送至脱硫剂再生池之中,经过还原反应得到NaOH,然后将回收的脱硫剂再次打入脱硫塔之中,通过洗涤方式有效脱除烟气之中含有的SO2物质。采用双碱法脱硫工艺时,其脱硫机理和石灰石/石灰—石膏烟气脱硫工艺较为相近。首先,先将烟气中含有的SO2物质溶于脱硫剂之中,在脱硫剂之中发生水解反应,得到H+以及HSO3-,其中H+和脱硫剂之中的OH-发生反应,并生成盐与水,这样便能够有效的促进SO2进一步溶解于脱硫剂中。经过脱硫反应得到的产物会被输送至再生池之中,再生池中含有另一种碱,通常采用Ca(OH)2,其会与脱硫反应生成物发生反应,这一反应便为脱硫剂的再生反应。脱硫得到的物质会以CaSO3以及CaSO4的形式析出溶液,再将得到的物质泵送到石膏脱水系统之中进行脱水处理,可以直接将得到的脱硫产物排出。再生池之中得到的NaOH能够被再次的利用,实现脱硫剂的循环使用目标。
3 脱硫除尘装置一体化改造分析
3.1改造设计的依据以及指标
锅炉系统的具体参数以及改造设计的各项指标见表1,表2。
表1锅炉系统具体参数
表2锅炉系统改造设计指标
3.2改造设计的原则
1)所采用的工艺技术应当先进且可靠,不仅要保证脱硫效率以及除尘效率,并且也要确保系统能够安全与稳定的运行,不会对系统有不良影响,得到了脱硫产物不能出现二次污染问题。
2)依照目前设备以及环境情况,尽可能的使用现有一些设备与装置,对设备及装置进行优化组合设计,形成具有较强针对性的改造方案。
3)因为现阶段煤炭资源较为紧张,煤炭燃料的品质不能得到有效保障,所以,在各种参数的确定工程中,对于控煤之前以及控煤之后具体煤质情况加以分析,合理确保各种参数。
4)经过技术改造以后,脱硫效率应当达到80%以上。
5)在设计脱硫设备过程中,要结合实际情况,尽可能的避免烟道出现折转现象,并且尽量降低烟道的长度,从而有效的减少排烟阻力。
3.3脱硫除尘一体化改造方案
1)在吸收塔装置之前竖井烟道位置处加设预增湿装置。
2)在烟气吸收塔装置之中加设旋转喷射装置,同时还需加设上旋流芯筒装置,确保烟气能够旋流效果更为理想。
3)利用双碱法脱硫工艺,不仅有效的去除烟气中SO2物质,同时确保脱硫剂能够回收利用,显著的解决脱硫成本,并且保证脱硫产物不会造成二次污染问题。
此次改造设计主要是为了确保锅炉脱硫的安全与可靠,并且全面考虑了改造方案的经济性以及环境效益。针对上述改造方案,做出如下说明:
1)在烟气吸收塔装置之前,加设旋涡预增湿脱硫除尘装置。在吸收塔装置之前竖井烟道位置处,对之前烟道麻石板进行一定的改造处理,新增设上预除尘设备,在该除尘设备之中加设多个旋涡式喷嘴装置,每一层设置两组。除尘使用水体经由喷嘴装置喷出并且雾化,向上进行喷淋作业,产生极其细微雾滴,确保除尘水能够和烟气之中包含粉尘更加充分的接触,有效的提升除尘效果。另外,还需要进一步的增加烟气的湿度,并适当降低烟气的温度,从而为之后开展脱硫作业提供有利条件。
2)在烟气吸收塔装置之中加设旋涡液柱喷射嘴,同时加设芯筒结构。在经由之前除尘装置预湿处理以后,此时烟气便会沿着烟道的切线方向而输送到主筒之中,即输送到吸收塔装置之中,完成初步除尘工作,将烟气之中包含的一些粉尘以及雾滴等加以去除。并且,为了能够进一步的增强烟气旋转效应,改善脱水以及除尘效果,还在吸收塔之中加设了芯筒结构。脱硫使用的液体经过喷嘴装置向上喷出,在上升以及下落的过程中,均能够有效的吸收烟气中SO2气体,并且还能有效的去除烟气之中的微小粉尘颗粒,从而有效的改善系统脱硫除尘效率。
4 改造后的效果分析
在对锅炉脱硫除尘装置进行改造之后,为了能够有效检查改造工作所拥有的效果,并且合理的确定改造后装置具体运行参数,依照各个运行工况,对系统做了全面的热态调试,在经过一系列调试之后得出下列结论:
1)通过对锅炉脱硫除尘装置的改造,虽然在一定程度上加大了烟气排出过程中存在的阻力,不过,并没有影响到锅炉正常的负荷能力,在经过改造之后,锅炉依旧可以满负荷的运行。
2)对改造实施之前以及改造实施之后进行对比分析发现,经过脱硫除尘改造后并未对锅炉的运行效率造成影响,也说明了脱硫除尘改造不会对系统的正常运行造成影响。
3)脱硫除尘装置在改造以后,其运行效率以及稳定性等均得以显著的提升。经过实际的试验测量得出,不管在任意一种工况之下,经过脱硫除尘改造之后所拥有的除尘效率均超过了99%。因为在整个试验过程中,所采用的燃料煤均为低硫煤,锅炉烟气中的含硫的浓度值最大是209mg/Nm3,经过折算之后脱硫效率达到82%。要是采用的燃料煤之中含硫量更好,则所得到的脱硫效率也会相应增加。
5 结语
在采用双碱法脱硫工艺之后,能够有效的对脱硫剂进行回收利用,从而可以降低脱硫过程中的原材料成本投入。并且,在装置改造之后,是采用液柱喷射的方法,在喷嘴位置发生结垢以及堵塞问题的概率非常小,并且脱硫过程产生的盐溶解度相对大,也会有效避免脱硫塔中发生结垢以及堵塞问题。通过预湿除尘装置能够起到除尘以及预湿效果,从而为后续脱硫以及除尘提供了极为有利的条件。脱硫之后得到的产物经过固液分离之后,溶液可以在此循环利用,避免出现二次污染物问题,具有良好的环境效益.
正确操作可确保干式吸尘器长时间稳定运行
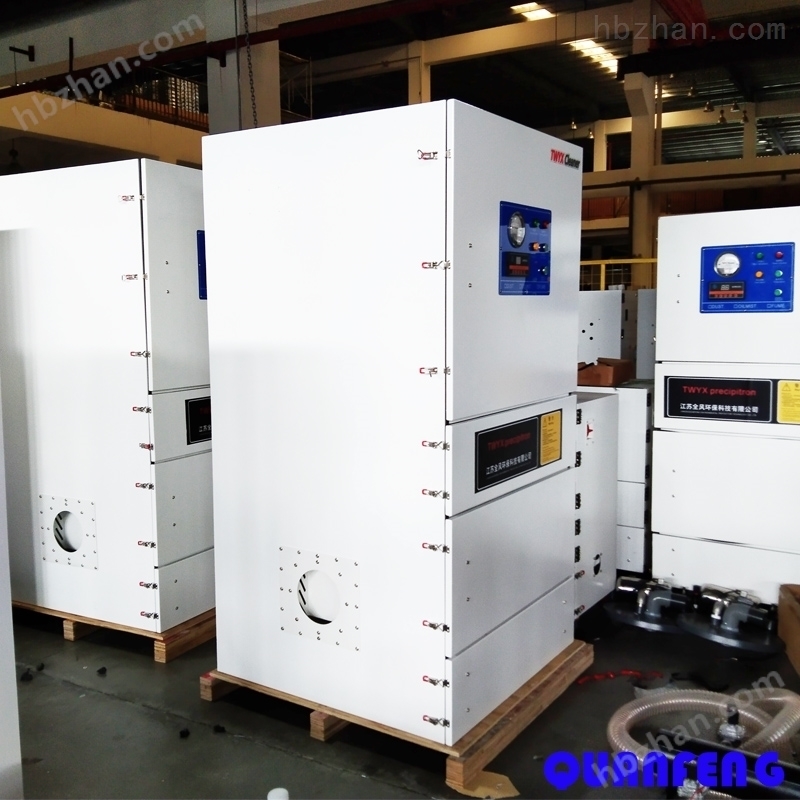
定期维护二级活性炭吸附箱可保护您享受清新健康的空气环境
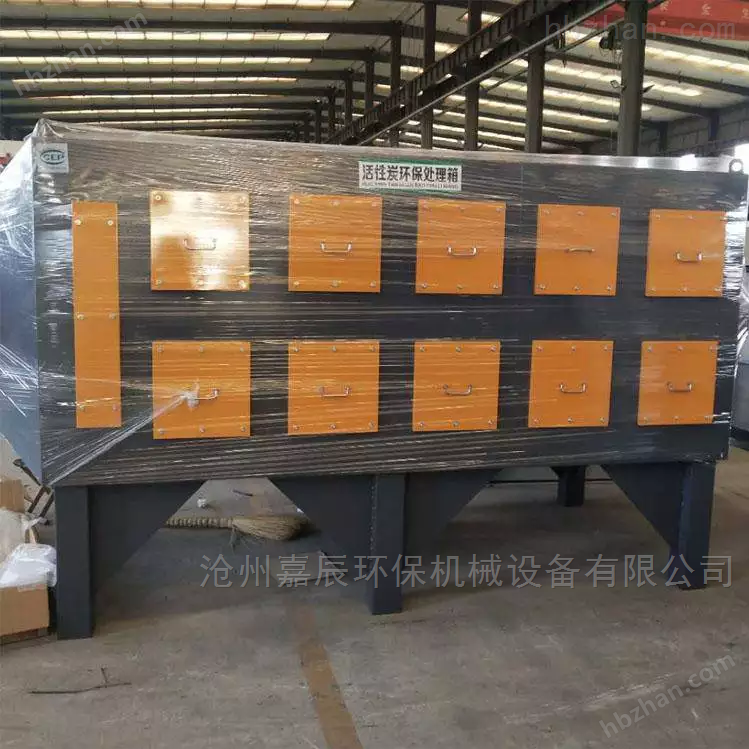